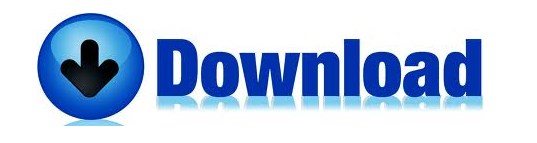

- #Gcode converter 3d print how to#
- #Gcode converter 3d print software#
- #Gcode converter 3d print code#
There are two Instructables which explain how to " get started with CNC" with fusion 360. And this is hard to manage for large/complex PCBs. However, all components/holes and traces must be created manually. In addition to etching and drilling, it is therefore also necessary to mill. This requires a hole with a diameter of 4 mm. These keys have a mount point for exact positioning. Secondly, it showed some 'problems' which would not have happened with regular components. And with a keyboard you want the keys to be exactly aligned. With a handmade PCB (etching and drilling) these holes will never be exactly in the right place. The choice of a keypad with Cherry keys has been a good choice for this Instructable.įirst, the keys must have exactly the same distances apart.

This is called ghosting and can be solved by adding a diode for each button. Pressing three buttons might result in detecting 4 buttons. But there is one problem with some combinations. And the program returns a value for each button. It is posible to press multiple buttons at the same time. This makes it possible to measure all values of the four buttons in row 1. The program starts with setting pin 5 to LOW.

They always return TRUE (1) unless they are connected to the GND or a LOW (output) pin. All input pins are defined as INPUT_PULLUP.
#Gcode converter 3d print code#
The code isn't optimized, which makes it very readable.
#Gcode converter 3d print software#
These 9 keys will be connected just like a 4 x 4 keyboard module.Īll keys are placed in a matrix, and it requires some software (or library) to read the keys with an Arduino. The sample project in this Instructable is a PCB board for a Cherry keys tester. This reduces cost, and I don't have to wait a few days for my PCB to arive. I'll be my own manufacturer, making the PBC. And from this point the course continues with selecting a manufacturer for the PCB. This is converted into a PCB design (lesson 3). In this course an electrical diagram is made in Autodesk Eagle (lesson 2). I started with the Circuit Board Design Class. This instructable uses the Autodesk Eagle PCB design tool. And after some iterations this results in a workable schedule for a prototype PCB. I usually make the design of an electrical diagram on paper. This won't be a fast and very strong CNC machine, but it should be capable of making PCBs. In this Instructable I combine these two items: Controlling a dremel with an Anet A8 printer. My previous Instructable was about creating and improving an Anet A8 3D printer. Unfortunately this router isn't accurate enough to make PCBs. I have some experience with hand routers, and I've made a drone frame with a dremel router once. That is why I decided to make PCBs using a CNC machine. And I would rather not use any chemicals. These will not be complex, just one or two layers. And for some future projects, I want to make small PCBs myself. It has been a few decades since I have designed and etched my last PCB. That is why I started researching how to make PCBs. It looks less messy, and reduces the chance of faults and defects.
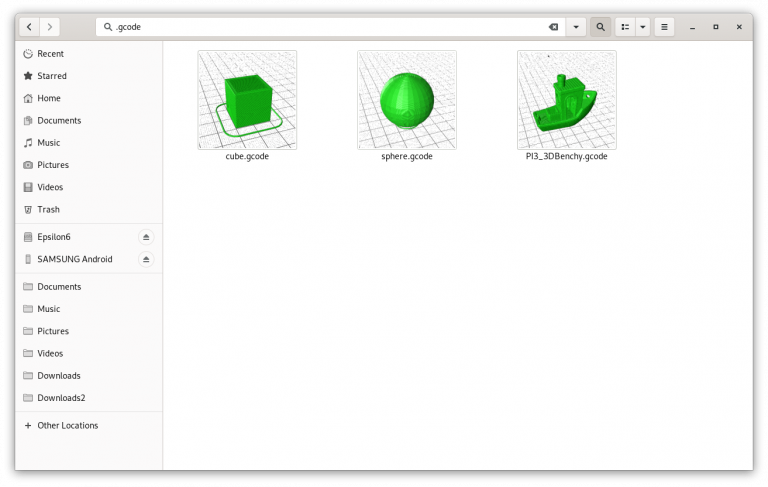
But creating a PCB yourself gives a project a more professional appearance. This works fine, and it's a quick way to finish a project. I've made a number of projects and Instructables with electronic circuits.
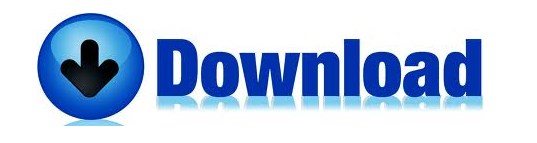